The part in question is a cylindrically symmetrical curve, with a cross section cutout listed as a profile of a line between point A<->point B. No datum structure on the control frame. Profile limit .060"
When getting a report trying to get a best-fit result, I usually expect the min and max values to be similar, and according to the online help https://docs.hexagonmi.com/pcdmis/2020.2/en/helpcenter/mergedProjects/core/geometric_tolerances/Profile_of_a_Line.htm
Setting min/max should find the smallest tolerance to fit all the points, but it shows -.016" to +.034" range.
The initial line of the report shows that it is only using .050" of the .060" tolerance but also is out of tolerance, not helping my confusion.
Taking the actual points reported and running them with the other softwares we have at our facility, I have more experience in and can get the even split of the deviations (-.023"<->+.019") or an overall lower profile (-.013"<->+.025") with another
So is there a simple answer to the following questions
1) is the profile good at the initial .050" reporting, even though it is listing it .004" over?
2) Is there a obvious reason that the min max in not having all the point inside the tolerance window.
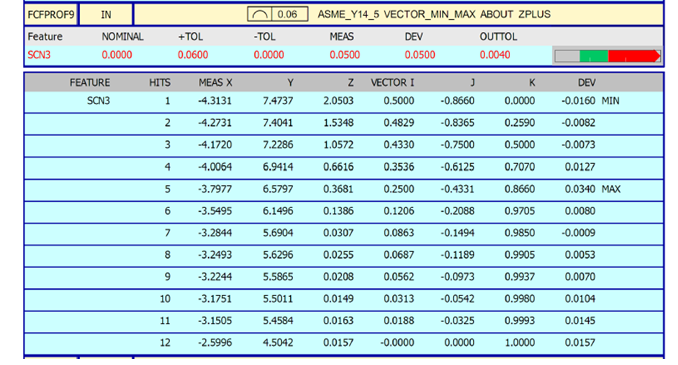