For this part, I would create a plane on the left end of the part, followed by cylinders for each straight. Then a plane on the right side. Next, I would construct a pierce point for plane 1 and cylinder 1 which would give me midpoint 1. Then construct an intersection point between cylinder 1 and 2, and that would be midpoint 2. I would continue this for the rest of the tube until i get to the last pierce point giving me midpoint 7. I have learned that i can create a cast point on cylinder 2, and it will give me midpoint 2.2; however, I have not yet been able to figure out a way of getting any of the x.1 midpoints.
That is where my question starts: How can i get these .1 midpoints? I feel like I've tried every combination of picking two cylinders and all the different types of points, and have had no luck in getting them. I have XYZ coordinates for these points, but more importantly, i have length-of-straights dimensions that are taken as a measurement between for example 1 to 2.1. This is a crucial measurement to the fit/form/function of our part, and as of now, i have absolutely no way of checking it.
My second question is this: Almost every part we have has a dimension for mid 1 to mid 7 across the Y-axis (as shown). But they will also dimension in this case, the top of cylinder 1 to the bottom of cylinder 7 (relative to the Y-axis) across the Y-axis. Every time i try to measure Cyl 1 to Cyl 2 across the Y-axis (with plus diameter getting me the closest), I never can seem to quite get a passable measurement.
Any help in either of these matters would be greatly appreciated.
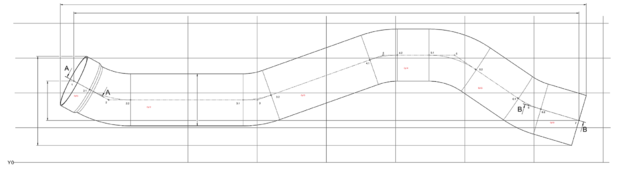