We sent the print to a gage supplier and they created the gage at Virtual condition. So essentially the Datum B locations are 17.149.( -0.01 for MMC and -0.01 for Perpendicularity) I understand how Virtual condition works and the concept behind it I believe but shouldn't the gage be made at 17.159 since that is the smallest diameter allowed? If the Datum B surface slants towards the smallest diameter the farthest point that it could slant would be a diameter of 17.159 right?
I understand Datum A plays a role in the additional tolerance but I can't seem to wrap my head around they why. Could anybody help me understand it?
This is a CMM check fixture. Datum A is 8 net pads around the bottom surface of a ring for Z. Datum B is 3 Blades that the part is rotated onto to control the XY. Attached is a picture of Datum B. Datum A is the underside of the Flat you see below the Blade rotation slot.
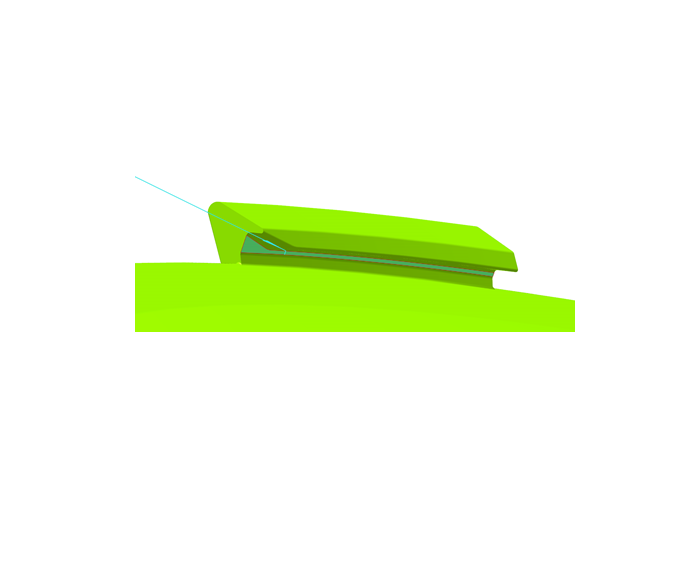