The part also only has one tiny slot to control rotation on one side of the part. So when placing the part on the gage it can rock, roll and slide everywhere. So that means I need to create local alignments on each clip to ensure that they hit correctly which means dancing around that almost crashing point the entire time. And I need to create alignment after alignment to ensure that I am hitting it correctly and then be sure that I recall a fixture alignment before proceeding because if I forget to revert back to the fixture and the next part changes in size/ location/ rotation by a mm or 2 I am guaranteed to crash. And this doesn't include the complexity of some of the dimensions and the callouts. For example a profile without datums with a unequal tolerance called out..... or a position on a single plane.....
So with all that being said I have been programming these parts for a couple weeks now and my head at the end of the day is just mush. That's where the Forum comes in. So I want to thank all of you for giving me a source of relief from my mental torture chamber over here.
Also, What are you more exhausting program memories. What is that one job that really kicked your butt?
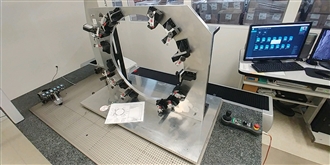