-first problem is If I stop the program in the middle of the loop, pcdmis thinks that the current piece whether it be 2,3,4,5,6 is the first piece to start on. I noticed that the actual coordinates on features are off and stuck. Why is that?
-after avoiding that, my Theo’s keep changing on me. I do not have CAD models so I have to change my Theo’s manually. After running the program they always keep changing. Any way to stop that?
-I guess I am just asking someone to take a look over what I have, I need some senior programmers to teach this young buck some knowledge please here is a picture of my set-up and some code … any advice will help and I am not afraid to take criticism
p.s. I left my manual alignment to show y’all how its changing up on me.
=ALIGNMENT/START,RECALL:USE_PART_SETUP,LIST=YES ALIGNMENT/END MODE/MANUAL MOVESPEED/ 100 FORMAT/TEXT,OPTIONS, ,HEADINGS,SYMBOLS, ;NOM,TOL,MEAS,DEV,OUTTOL, , LOADPROBE/LLDAWG_TIP1 2X30 TIP2 3X50 TIP/TIP1, SHANKIJK=0, 0, 1, ANGLE=0 MAN_PLNA =FEAT/PLANE,CARTESIAN,TRIANGLE THEO/<10.39954,-0.91716,-27.00211>,<0,0,1> ACTL/<10.29746,-0.85066,-27.00047>,<0.0000813,-0.0034436,0.9999941> MEAS/PLANE,4 HIT/BASIC,NORMAL,<2.24446,-0.9518,-26.99909>,<0.0002452,0.0062019,0.9999807>,<2.89135,-0.58091,-27.00009>,USE THEO=YES HIT/BASIC,NORMAL,<10.61085,-1.27203,-27.00125>,<0.0002452,0.0062019,0.9999807>,<18.65044,-0.42268,-26.99876>,USE THEO=YES HIT/BASIC,NORMAL,<16.79155,-0.97871,-27.00204>,<0.0002452,0.0062019,0.9999807>,<13.03635,-1.1995,-27.00427>,USE THEO=YES HIT/BASIC,NORMAL,<11.95131,-0.46609,-27.00607>,<0.0002452,0.0062019,0.9999807>,<6.6117,-1.19955,-26.99876>,USE THEO=YES ENDMEAS/ $$ NO, A1 =ALIGNMENT/START,RECALL:STARTUP,LIST=YES ALIGNMENT/LEVEL,ZPLUS,MAN_PLNA ALIGNMENT/END COMMENT/OPER,NO,FULL SCREEN=NO,AUTO-CONTINUE=NO, ALIGNMENT MAKE LINE ON Y-MINUS/FRONT $$ NO, MAN_LINEB =FEAT/LINE,CARTESIAN,UNBOUNDED THEO/<2.95008,-1.28824,-27.17141>,<1,0.0000004,0> ACTL/<2.24178,-1.54568,-27.14377>,<0.9999997,-0.0008179,0> MEAS/LINE,2,ZPLUS HIT/BASIC,NORMAL,<2.95008,-1.28824,-27.17326>,<-0.0008712,-0.9999996,0>,<2.24178,-1.54568,-27.14469>,USE THEO=YES HIT/BASIC,NORMAL,<18.51021,-1.3018,-27.16955>,<-0.0008712,-0.9999996,0>,<19.00739,-1.55939,-27.14285>,USE THEO=YES ENDMEAS/ $$ NO, A2 =ALIGNMENT/START,RECALL:A1,LIST=YES ALIGNMENT/ROTATE,XPLUS,TO,MAN_LINEB,ABOUT,ZPLUS ALIGNMENT/END MAN_PNTC =FEAT/POINT,CARTESIAN THEO/<1.99161,-0.72581,-27.07116>,<-1,0.0000022,0> ACTL/<1.98758,-1.25369,-27.14727>,<-0.9999969,0.0009674,0.0022823> MEAS/POINT,1,WORKPLANE HIT/BASIC,NORMAL,<1.99161,-0.72581,-27.07116>,<-1,0.0000022,0>,<1.98758,-1.25369,-27.14727>,USE THEO=YES ENDMEAS/ $$ NO, A3 =ALIGNMENT/START,RECALL:A2,LIST=YES ALIGNMENT/TRANS,ZAXIS,MAN_PLNA ALIGNMENT/TRANS,YAXIS,MAN_LINEB ALIGNMENT/TRANS,XAXIS,MAN_PNTC ALIGNMENT/END $$ NO, $$ NO, C1 =COMMENT/INPUT,NO,FULL SCREEN=NO, what serial number is this? $$ NO, ASSIGN/VCOUNT=0+C1.INPUT $$ NO, MODE/DCC $$ NO, $$ NO, $$ NO, $$ NO, V2 =LOOP/START,ID=YES,NUMBER=3,START=1,SKIP=, OFFSET:XAXIS=0,YAXIS=18.25,ZAXIS=5,ANGLE=0 V1 =LOOP/START,ID=YES,NUMBER=3,START=1,SKIP=, OFFSET:XAXIS=0,YAXIS=6,ZAXIS=0,ANGLE=0 MODE/DCC $$ NO, DISPLAYPRECISION/4 FASTPROBEMODE/ON MOVESPEED/ 300 PREHIT/0.1 RETRACT/0.1 TRACEFIELD/NO_DISPLAY,LIMIT=15 ; P.O. : TRACEFIELD/NO_DISPLAY,LIMIT=25 ; DRAWING NUMBER : TRACEFIELD/NO_DISPLAY,LIMIT=15 ; INSPECTOR : TRACEFIELD/NO_DISPLAY,LIMIT=15 ; JOB NUMBER : TRACEFIELD/NO_DISPLAY,LIMIT=15 ; HEAT NUMBER : TRACEFIELD/NO_DISPLAY,LIMIT=15 ; VIN NUMBER : TRACEFIELD/NO_DISPLAY,LIMIT=15 ; CUSTOMER : TRACEFIELD/NO_DISPLAY,LIMIT=15 ; SERIAL NUMBER : VCOUNT MOVE/POINT,NORMAL,<-0.1515,0.5576,0.3125> $$ NO, PLNA =FEAT/PLANE,CARTESIAN,TRIANGLE THEO/<8.4562,0.6582,0.0018>,<-0.0003726,0.0020609,0.9999978> ACTL/<8.4563,0.6577,-0.0255>,<-0.0003947,0.0122227,0.9999252> MEAS/PLANE,6 HIT/BASIC,NORMAL,<0.1267,0.6388,0.0005>,<-0.0003726,0.0020609,0.9999978>,<0.1268,0.6387,-0.0391>,USE THEO=YES HIT/BASIC,NORMAL,<4.7994,1.0227,0.0027>,<-0.0003726,0.0020609,0.9999978>,<4.7995,1.0226,-0.0492>,USE THEO=YES HIT/BASIC,NORMAL,<11.7019,1.0676,-0.0009>,<-0.0003726,0.0020609,0.9999978>,<11.702,1.0675,-0.0561>,USE THEO=YES HIT/BASIC,NORMAL,<17.7592,0.4945,0.0109>,<-0.0003726,0.0020609,0.9999978>,<17.7593,0.4944,-0.0396>,USE THEO=YES HIT/BASIC,NORMAL,<11.9732,0.6058,-0.0022>,<-0.0003726,0.0020609,0.9999978>,<11.9733,0.6057,-0.0538>,USE THEO=YES HIT/BASIC,NORMAL,<4.3769,0.1195,0>,<-0.0003726,0.0020609,0.9999978>,<4.377,0.1194,-0.0252>,USE THEO=YES ENDMEAS/ MOVE/POINT,NORMAL,<-0.1431,-0.1238,0.2051> $$ NO, LINB =FEAT/LINE,CARTESIAN,UNBOUNDED THEO/<0.6638,0.0267,-0.0699>,<1,-0.0000939,0> ACTL/<0.6638,0.0318,-0.0697>,<1,0.000208,0> MEAS/LINE,2,ZPLUS HIT/BASIC,NORMAL,<0.6638,0.0267,-0.0719>,<-0.0000939,-1,0>,<0.6639,0.0318,-0.0717>,USE THEO=YES HIT/BASIC,NORMAL,<17.5832,0.0251,-0.0679>,<-0.0000939,-1,0>,<17.5833,0.0353,-0.0677>,USE THEO=YES ENDMEAS/ MOVE/POINT,NORMAL,<-0.2919,-0.3716,-0.0759> PNTC =FEAT/POINT,CARTESIAN THEO/<-0.0107,0.2214,-0.0721>,<-1,0.0000022,0> ACTL/<-0.0107,0.2214,-0.0721>,<-1,0.0000022,0> MEAS/POINT,1,WORKPLANE HIT/BASIC,NORMAL,<0.0002,0.2213,-0.0723>,<-1,0.0000022,0>,<-0.0107,0.2214,-0.0721>,USE THEO=YES ENDMEAS/ $$ NO, PREHIT/0.06 RETRACT/0.06 A4 =ALIGNMENT/START,RECALL:A3,LIST=YES ALIGNMENT/LEVEL,ZPLUS,PLNA ALIGNMENT/ROTATE,XPLUS,TO,LINB,ABOUT,ZPLUS ALIGNMENT/TRANS,XAXIS,PNTC ALIGNMENT/TRANS,YAXIS,LINB ALIGNMENT/TRANS,ZAXIS,PLNA ALIGNMENT/END $$ NO,===================================================== GRP1 =GROUP/SHOWALLPARAMS=NO HAD TO CONDENSE THIS ENDGROUP/ID=GRP1 @@@@@@PROGRAM@@@@@@@ $$ NO,===================================================== C2 =COMMENT/YESNO,NO,FULL SCREEN=NO,AUTO-CONTINUE=YES,TIME DELAY=5, KEEP GOING? $$ NO, IF_GOTO/C2.INPUT=="NO" ,GOTO = L1 $$ NO, ASSIGN/VCOUNT=VCOUNT+1 $$ NO, [ATTACH=CONFIG]9069[/ATTACH] TRACEFIELD/NO_DISPLAY,LIMIT=15 ; SERIAL NUMBER : VCOUNT REPORT/LABEL, FILENAME= PPAP ITEM DIMENSION (2) NOT COPY.LBL $$ NO, L1 =LABEL/ $$ NO,
Attached Files
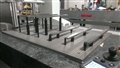