Saturday morning, New customer, and PPAP being setup to run for next week, and one GD & T callout that leaves me scratching my head!
The attached drawing shows the 40.8 Ø (+ draft (3° per notes is draft)) on a cast OD with a profile of 3.6 and according to the control plans Engineering sent down on the inspection plans this is being called out to check as true position of 1.8 back to -D-.
I've never seen profile of a surface called out to an OD (especially a cast OD) so what am I looking at here? Reading the GD&T book this late in the morning (I'm third shift) is not helping. Near as I can figure out with the book I'm looking at checking this cast surface with a circle in two or three spots and just figuring out what the high and low spots would be trig'ing out the possible largest diameter. Or should I check with a line on the OD and figure/report where the tangent points on the line lay within the surface profile?
Any thoughts / suggestions?? I Just need to make sure that we are reporting this for the PPAP, and subsequently an annual dimensional report for the most part given that it is a cast feature, but I want to make sure that it is correct too. I'll be back in tonight to work on this so any help from you weekend warriors would be wonderful! Thanks!
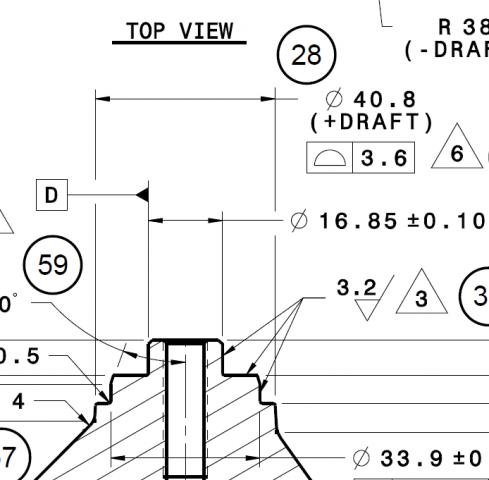