Do i need the od dat to be a cylinder or a circle?
Does it matter if its a constructed cyl or an auto cyl?
My dat c is a constructed width, should it be the line instead?
I added two pictures if that helps
please help!!
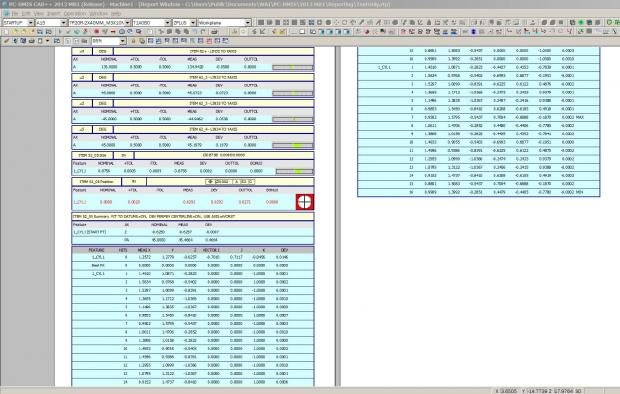

Your Products have been synced, click here to refresh
No name calling from me, just trying to understand your reasoning. I like to learn something new every day, so this is something new to me. I think if you do some digging, was it Josh Carpenter(sp?), posted an explanation of datum shifts and the Xact measure position output.
the actually call out is TP .002 |A|B|C|
Yeah there should be four, I just have the one in it so its easier to manage tell I figure out how to get the dimensioning correct. Does it matter about my alignment? Do I need to level to the OD cyl dat-b?
or is leveling to the top plane dat-a the same?
What technique are you using to rotate with the datum C slot?
You want to try this
Take multiple points along the slot length, top and bottom of slot.
Use those points with a best fit ROTATE ONLY method.
Then remeasure the slot for position and width.
I was assuming that A and B were already aligned.
Is this your argument?
Its not an argument, it a fact. If you do not have a -C- Slot, the you could do the BF rotate ONLY, but since you have a specific -C- that locks 2 DOF, you are not allowed to perform a BF any longer
I am measuring this part right now this is a cylinder about 3 inches tall. The od is dat-b. The top plane is dat-a and dat-c is a slot in the center of the part. The part has 4 counter bore holes along the side of it every 90 degrees. Here is a picture of what the result looks like, and i know its wrong.
Do i need the od dat to be a cylinder or a circle?
Does it matter if its a constructed cyl or an auto cyl?
My dat c is a constructed width, should it be the line instead?
I added two pictures if that helps
please help!!
© 2024 Hexagon AB and/or its subsidiaries. | Privacy Policy | Cloud Services Agreement |