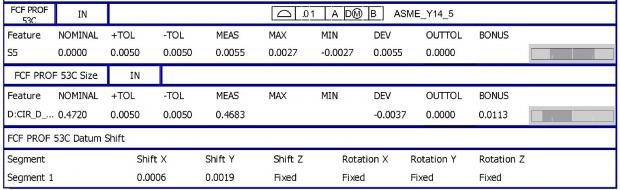
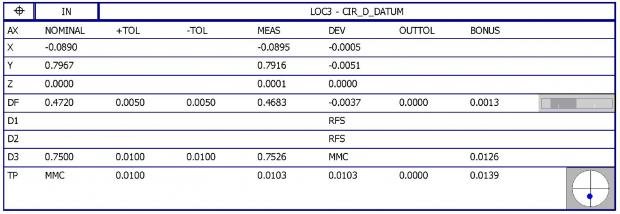
Your Products have been synced, click here to refresh
Go to your the profile dimension and turn GRAPH=ON then MULT=100.
this will show you where the hits you are taking are showing up on the CAD model.
with a profile of .010 you have a +/-.005 on both sides of the imaginary "nominal" surface. if your max hit is -.0035 from nominal and your other MIN hit is .002 from nominal you have a total of .0055 profile but you never break out of your +/-.005 profile tolerance.
in your case your max/min values are .0027. combined that gives you a total profile of around .0055
BONUS tolerance is applied when you are figuring MMC/LMC.
http://www.toolingandproduction.com/qim/0205bonus_tolerances.aspx
since your D3 feature is MMC, nominal is .750 +/-.010 and the feature measure .7526 (a difference of .0026), you can add that the to true position tolerance of .010, effectively making it TP .0126. (the spec is ALLOWING you some extra BONUS room to play with since your .750 feature is not "MAXED" out on it's size.)
continue to apply the same thing to the other diameter feature, add them together and that's your total bonus tolerance.
is it me or does the link not work?
I'm interested in finding out how pcdmis is calculating true position if a datum is called out to have MMB.
© 2025 Hexagon AB and/or its subsidiaries. | Privacy Policy | Cloud Services Agreement |