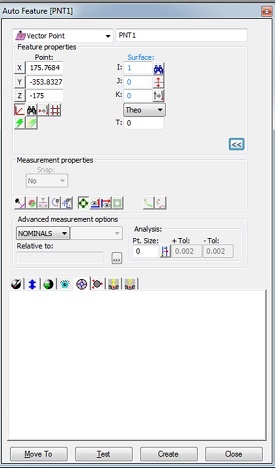
Your Products have been synced, click here to refresh
If I'm understanding right then it would be helpful to have it on if I am reporting the deviation of vector point that is normal to a surface in one axis.... 0,0,1 for example rather than say.... .2551,.36666,.754444. Hope that made sense.
© 2025 Hexagon AB and/or its subsidiaries. | Privacy Policy | Cloud Services Agreement |