From the book of Matthew:
Try all of this:
Alignments:
First of all, to do ANY alignment, 3-2-1 or iterative, you MUST have XYZ values for whatever you use for the alignment.
Step #1
Do this no matter WHAT type of alignment you are going to do.
1) Place the part on the table the way it will sit for your inspection
2) Import your model data BEFORE you do any measuring
3) Using the CTRL-F3 option (3-D rotate), rotate the cad data until it matches the way the part sits on the machine, remembering that as you look at the screen you are looking DOWN on the machine
4) Once you have the cad data rotate (you are actually ONLY rotating the VIEW of the cad data), use F5 to open the setup options.
5) Go to the Part/Machine tab and while looking at the 3-D rotate cube, set your CAD to MACHINE axis
6) Click OK
7) Set your workplane to the top of the cube (if the top, facing YOU face of the cube is X-, use the X- workplane)
.
When I complete step 6) the model flips back to it's original orientation. Should this happen? If I continue through the rest of Matt's steps for aligning it and then do a CAD=Part it is still misaligned like step 5) had no effect. I'm programming offline. Thanks in advance for any help.
Attached Files
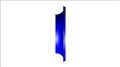