I have a bit of a strange problem with scanning and I hope maybe one of you guys knows the solution or gets me on the right track.
I have 3 different machines and an offline station.
1x Leitz PMM-C
1x DEA Global Advantage
1x Tigo SF
1x Offline
For each of these machines I have a template routine with their respective parameters saved first thing in the program. Attached you can see the template routine for the Tigo. As you can see I have the “optionprobe” command who sets the relevant offset forces.
If I create routines on the machines with the respective template everything works fine. The scans run smoothly with the correct offset force.
The problem appears when I create routines on the offline station. I open the template of the machine I plan to run the routine and create the routine normally. Now when I run the routine on the machine some scans use wrong offset forces. I can visibly see the probe driving too much into the part at the start of the scan and then recovers back a bit. When I evaluate the form of the scanned feature I see a deviation where the scan starts pointing into the material. Which confirms what I see when the scan starts. Going into the scan and recreate doesn’t solve this problem, only when I create the scan from scratch and delete the old one, the scan works fine.
We use mainly 2 scan types. The basic circle scan and the linear open scan. We don’t use the adaptive scans. The problem only affects the circle scan, the linear open scan works just fine.
Oh and one more strange thing. The problem only affects the Global and the Tigo. The Leitz machine doesn’t care.
Do you guys have any idea why this could happen?
Like this there is not much time saving if I have to recreate most of the scans and then go into every feature to link it to the new scan.
Thanks in advance for your help guys
Attached Files
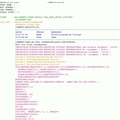