I need help. I've received a ASME drawing in inches from a client (i usually work on ISO and with mm) and they've demanded that I measure a position with the MMC condition in the hole and for each datums (B and C).
The thing is that i don't know what values i have to put in the datum MMC size and why the third datum (C) appears like a plane in the repport when actually is a hole?
What i need to know is what values do i have to put in the datum MMC size and why the third datum have to be a plane for pc-dmis?
Attached is
Thanks in advance.
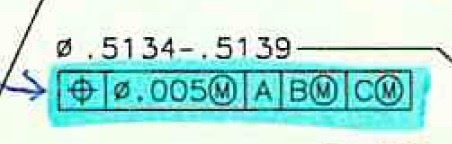
Attached Files
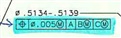