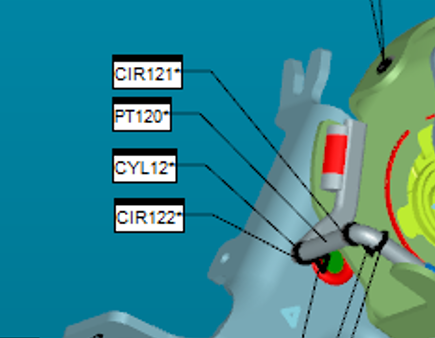
I learned from 101 that for cylinder, the probe should vertical touch the point ( we use analog probe with 2 mm header), the first 3 or 6 even 8 points compose a plane. I believe this definition is good for compensation of the probe header. Now we have a product with an around 5 mm diameter wire which welds on the part. On the drawing the wire could have 2 mm center variation on one workplane. The program measures it as a cylinder( touch 8 points in 180 degree) with a fix angle which I believe has 10 degree away from vertical cut the cylinder (around 80 degree to the plane). I wonder how much variation does this measurement bring it due to my concern and anything we could help reduce those kind of variation?
Thanks