I have essentially a block that has Z+ plane as Datum A, X-axis is a midplane from a basic dimension, Datum B, Y-axis is a midplane from basic dimension, Datum C (practically on the CMM I am doing Plane, LineX, LineY, then intersection of lines for origin) with a hole that's True Position is relative to A|B|C, which gets defined as Datum D.
There's a second hole (technically a slot but the engineer said he's more concerned about the center point) that has a TP referenced to Datum A|D.
See my attached """""""drawing"""""""" (I'm not a drafter so I hope it makes sense).
Basically the engineer described it to me as saying the Datum D hole is positioned relative to the outer dimensions (and flat plane of A) of the device, then the second hole is "clocked" to the Datum D hole along those XY coordinates.
My question is the theoretical position of the slot based off the actual measured position of Datum D or the theoretical position? e.g. if Datum D THEO XY X=20 Y=80 | ACTL XY X=20.01 Y=80.01 is the X=40 Y =70 slot THEO dimensioned from the THEO or ACTL of Datum D? If I understand how true positioning works (I don't), the theo position of the slot needs to be in reference to the measured position of Datum D, because if you reference it to the Datum D theo you are adding the variance allowed in Datum D's position.
(I apologize this is a simple question but I'm an EET landed with the role of getting our CMM going again and spatial geometry was not my strength. We use OpenDMIS so I understand the specific program terminology is different but I've been figuring out how to program it by learning PC-DMIS from posts here then translating it to OpenDMIS. To save you that burden, answer as if I'm using PC-DMIS.)
Thank you!
Attached Files
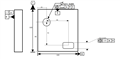