i got a measuring/construction/engineer/noob problem.
i have this small 40 degree, 2 degree conical thing, that is supposed to have a diameter 6.86mm where it is as smallest, and its supposed to be centered in the casted hole(D), and perpendicular to the plane(A)
i dont know how to measure it, since its a very small surface, and its also not cylindrical, its conical with a 2degree angle.
so i have to measure it as a cone. and then construct a circle using cone feature, but the results are very unsure.
the matching part has the exact same feature, except its internal, and it should run free over the tap thingy.
how can i measure it
or how would u else dimension it, so that the matching part fits.
ty all, thanks for ur feedback
Attached Files
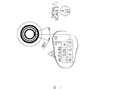
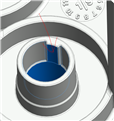