

The odd thing about this part are the position callouts; there is no MMC on the hole dimensions themselves, but there is on BOTH datums, even though the positions for the datums themselves have no MMC callouts. That alone (I think) is improper, and I'm fairly certain that the dimensioning was probably done by a clueless summer intern. But, now
I have to deal with it.
As an example, I'm showing the edit window for the position callout for the "22x" callout in the center of the other pic. All the unPEM'ed holes, whether datums or not, are Ø10mm +.3/-.1. Most of them run around 10.05mm, so my 'bonus tolerance' usually runs about .15 from any datum called out.
First question I have is this: Am I setting it up properly? Up in "Feature Control Frame Editor" window, is it correct that I enter the diameter of the datum at it's MMC value (being 9.9mm)? Or was I supposed to enter something else?
My second question (and the most important) is this: Why isn't the software calculating my position dimension actually using the bonus tolerance from the callout? When I calculate those 22 holes, no bonus tolerance is added, but at the end of the calculation, it does tell you what the bonus from the secondary and tertiary datums are, but it just doesn't use that info in the calculations. Am I missing something in my setup? Is there something in the "advanced" tab that can help me? Or, is this something that only an upgrade to a newer model of DMIS is going to fix?
Attached Files

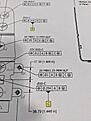

