Attached is a rough sketch of the print (everything, but hole positions and Basic dimensions were removed). I certainly get the design intention, and the GD&T kind of makes sense as well. The design intends for the top holes on Datum C to be within XXX position of the Datum B hole pattern (located on Datum A)
Am I doing something wrong? Is the GD&T wrong? If it is wrong, why is it wrong and how can it be corrected? I talked with the design engineer behind this part and they think that they GD&T is correct, so I'd definitely need a strong argument to make any sort of print change.
Sorry for the rambling, I hope it all makes sense!
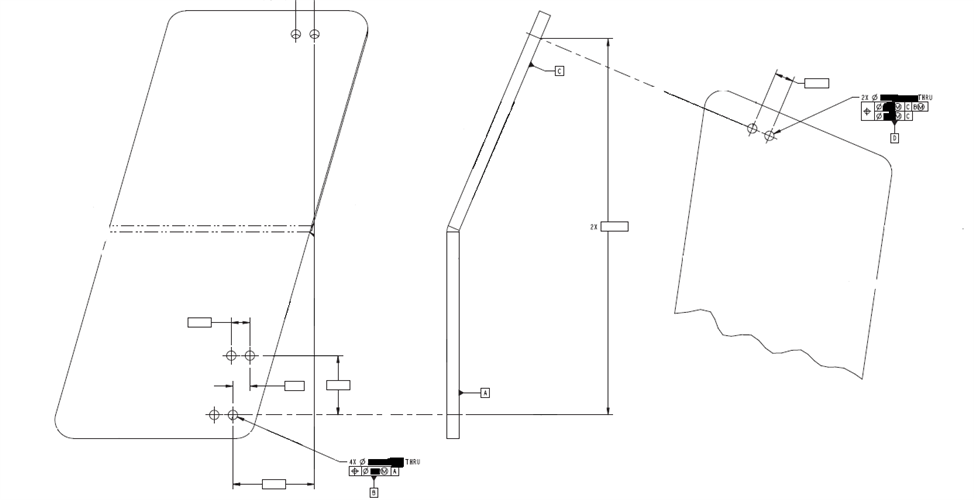