The part is a car door.
Legacy datum is an iterative alignment using 4 separate planes to level to (A).
A circle (B) and round slot (C) to rotate around.
And that same circle (B) to origin to.
Using that alignment our largest deviation for this section (C to D) of vector points is ~3.4mm
When using GeoTol the result is 7.4mm
For geotol I:
Created a primary datum plane and called it A
Defined that new plane as A
Defined B as the circle B
Defined C as the round slot C
I created a data set of the 42 points that make up section C to D and set up the FCF just like the callout on GD&T.
A =FEAT/PLANE,CARTESIAN,OUTLINE,NO
THEO/<3138.512,807.3,1054.12>,<0,-1,0.0000001>
ACTL/<3138.534,808.522,1054.166>,<-0.0001932,-0.9999999,0.0003738>
CONSTR/PLANE,PRIMARY_DATUM,A1,A2,A3,A4,,
MATH_TYPE/CONSTRAINED_L2,BFRE
DATDEF/A,FEATURES=A,,
DATDEF/B,FEATURES=B,,
DATDEF/C,FEATURES=C,,
GAP_C_D =FEAT/SET,CARTESIAN
THEO/<2597.195,931.591,1059.523>,<0,0,1>
ACTL/<2594.191,931.69,1059.54>,<0,0,1>
CONSTR/SET,BASIC,GAP_01,GAP_02,GAP_03,GAP_04,GAP_05,GAP_0 6,GAP_07,GAP_08,GAP_09,GAP_10,GAP_11,GAP_12,GAP_13 ,GAP_14,GAP_15,GAP_16,GAP_17,GAP_18,GAP_19,GAP_20, GAP_21,GAP_22,GAP_23,GAP_24,GAP_25,GAP_26,GAP_27,G AP_28,GAP_29,GAP_30,GAP_31,$
GAP_32,GAP_33,GAP_34,GAP_35,GAP_36,GAP_37,GAP_38,G AP_39,GAP_40,GAP_41,GAP_42,,
MOVE/POINT,NORMAL,<-1169.71,1657.333,1951.929>
GAP_CD =GEOMETRIC_TOLERANCE/STANDARD=ASME Y14.5,SHOWEXPANDED=YES,
DATUM_MATH=DEFAULT,DISPLAY_COORDS=DRF,
UNITS=MM,OUTPUT=NONE,ARROWDENSITY=100,ITERATEANDRE PIERCECAD=YES,
SEGMENT_1,PROFILE_SURFACE,1.4,__,A,B,MMB,<size>,__ ,C,MMB,<size>,__,
TEXT=ON,CADGRAPH=OFF,REPORTGRAPH=OFF,MULT=10,
MEASURED:
GAP_C_D:7.442,
SEGMENT_2,PROFILE_SURFACE,COMPOSITE,0.8,__,<dat>,< dat>,<dat>,TOL_ZONE_MATH=DEFAULT,
TEXT=ON,CADGRAPH=OFF,REPORTGRAPH=OFF,MULT=10,
MEASURED:
GAP_C_D:0.439,
ADD
DATUMS/REPORTDATUMSIZE=OFF,
B(B):NOM=19,+Tol=0.1,-Tol=0.1,
C(C):NOM=19,+Tol=0.1,-Tol=0.1,
FEATURES/GAP_C_D,,
Attached Files
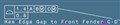