I have a small part that I'm inspecting and the only way I can probe it is to go around the part at 4 different angles using cones.
What I'm doing is, pretend that these cones are 90° included. I'm setting my probe angle to A45B0, probing the cones, then A45B90, probing the cones, A45B-90, probing the cones, then finally A45B180 and probing the final cones. After this, I create a constructed set using all the cones and dimension them with a profile tolerance(.002'). Now from what I can see, our parts look good, in terms of angles and position, but for whatever reason the profile tolerance is out of tolerance.
Is this the best method to use to inspect these features?
Is there a way to combine these cones in order to use the measured points into a larger cone?
Example of the part (Not the actual part):
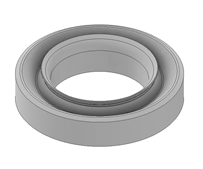
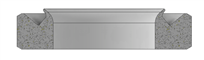
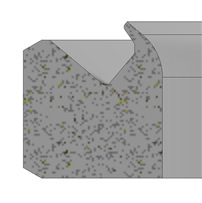