I am looking for some input on how you would program this. Datum A is the midplane of the part using target points at specified locations from Datum B. It doesn't help that Datum C makes zero sense hah, so I left it off of my drawing. I am pretty lost in terms of how to do this correctly (iterative alignment?)...at this point I'm am considering just making planes (with many hit points) and a midplane for Datum A.
Attached Files
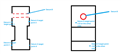