It is legal per ASME Y14.5-2018. section 11-8 "COMBINED CONTROLS" and figure 11-29.
But, my question is how would somoene accomplish this in PC-DMIS.
Sorry, but I've never had to inspect this call-out, and originally thought it was just BS.
Sorry if I posted something incorrectly, it's been awhile since my last post.
Thank you in advance.
Attached Files
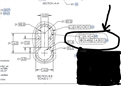