Just trying to figure this out - when I dimension a circular feature I'll get one size but when adding a GD&T dimension for that same exact feature I get a different size altogether (example below). What's the reason for this?
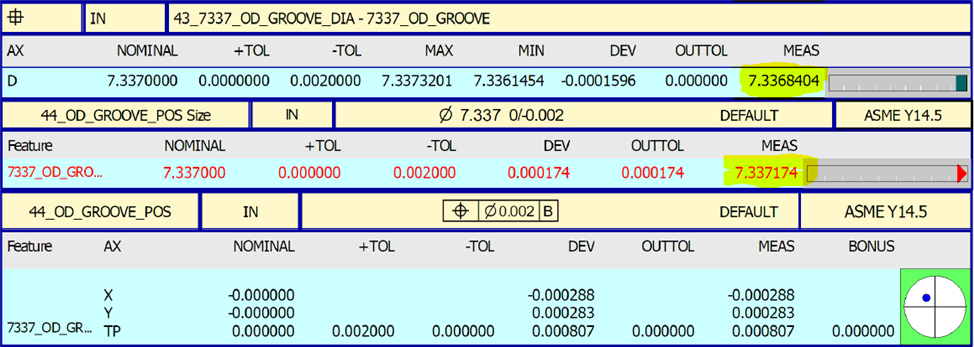
Your Products have been synced, click here to refresh
© 2025 Hexagon AB and/or its subsidiaries. | Privacy Policy | Cloud Services Agreement |