I've staged the part and aligned with the bottom as -A- (level and origin Z).
I probed and created 4 cylinders, then created circles at the intersections of the cylinders and -A- respectively, then used the circles to create one circle -B- and translated X,Y to -B-.
I probed plane -C- and controlled rotation around Z with plane -C-.
My question is; How is the true position calculated / reported in this case, when there are multiple holes making up one datum in reference to a plane only?
Thanks.
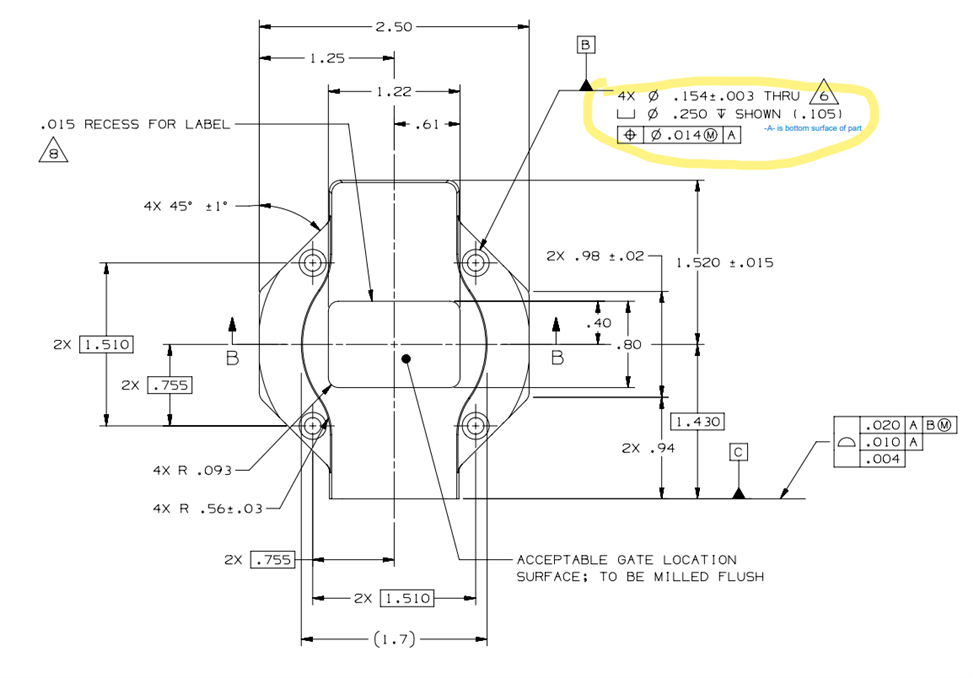
Attached Files
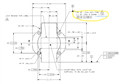
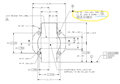