I have a large plate which has features on both sides that need checking. At the moment I'm picking up my CMM bed (Z Plus), the central bore, and a finished edge (XPlus)
My question is, when creating the new alignment after I have flipped over the plate, should I be picking up the granite again or should I be picking up the (now top) surface of the plate? Further, should I be picking everything up in exactly the same way? Meaning, should my XPlus edge now be facing XMinus, and should I call it out that way in the alignment? As written, I'm interpreting it as "Pick up the surface of the plate and align it to ZMinus since in the first orientation it was the granite plate in the ZPlus. Then pick up the finished edge in the same direction you picked it up the first time which is now XMinus. Align the features as ZMinus and XMinus since that would match the original alignment."
I have a feeling I'm over thinking this pretty hard. I've been fiddling with it for a little while now, but I can't seem to get it to work. I uploaded a picture of the two alignments.
Attached Files
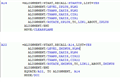