I have the following measurement to do 12.4 (mm):
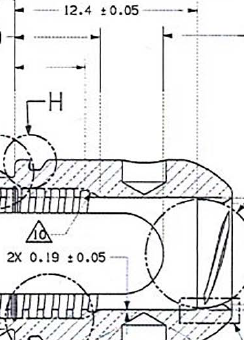
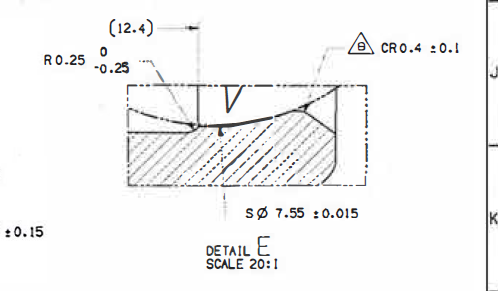
The idea is to use the CMM as a profilometer. Having located and measured the Sphere 7.55, I could zero on it and take a circle in the cross section shown in the second pic. Normally when the probe goes from reading PR 7.55/=3.775mm or whatever the actual DIA is there to something else, I could locate the point where the transition is happening. I am not familiar with T values but I suspect I could also use these somehow. The probe I have available to reach that point is a 6dia ruby ball that looks something like this:
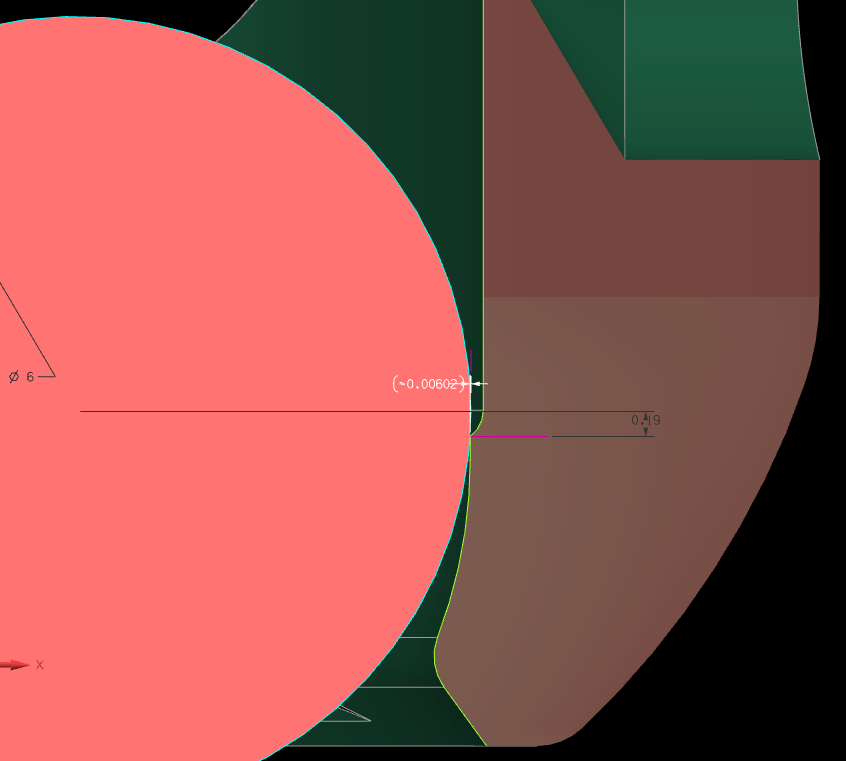
Due to dimensions being so small there, I searched in the cad the point of 0.006mm where the PR will be bigger and the idea is locating this point and substracting 0.19 to find my transition value of 12.4
How would you guys handle that? Performing a scan and using arrays seemed to be to much for me as populating arrays in PCdmis seems to be a PITA. Thanks in advance for your inquires!
Attached Files
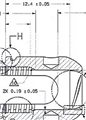