I'm sure this question has been answered a million times on here, but I couldn't find specifics of my situation during a search. At out shop, we have 2 Global 5.5.5 CMMs that use the Hexagon/Tesa touch trigger probe system. With that said, I'll tell you how we calibrate the probes here. Both CMMs have a sub-plate. We screw the calibration sphere in the same location every time we calibrate. We will write a simple calibration program for all part numbers, so if me or the QE isn't here, they can screw in the calibration sphere, and open the program to calibrate. We use parameter sets for each part number, so we don't have to calibrate all tips. For every tip we use, we always say "No" when PCD asks if the calibration sphere has moved. Can we loose accuracy by doing this? My QE says that since we never move the actual location on the subplate, it shouldn't matter.
Also, we use one of our commonly used tips (1mm X 27.5mm A0B0) for the master probe, but we never use it to find the sphere (as its always placed in the same place on the subplate.
Here is the code for our typical calibration program:
STARTUP =ALIGNMENT/START,RECALL:USE_PART_SETUP,LIST=YES ALIGNMENT/END MODE/MANUAL FORMAT/TEXT,OPTIONS,ID,HEADINGS,SYMBOLS, ;NOM,TOL,MEAS,MAXMIN,DEV,DEVANG,OUTTOL MOVESPEED/ 300 COMMENT/OPER,NO,FULL SCREEN=YES,AUTO-CONTINUE=NO, MOVE THE PROBE UP ABOVE AND OUT OF THE WAY IN A SAFE POSITION. COMMENT/OPER,NO,FULL SCREEN=YES,AUTO-CONTINUE=NO, REMOVE ALL FIXTURES AND PARTS FROM THE TABLE. PLACE THE CALIBRATION SPHERE IN LOCATION I9. FORMAT/TEXT,OPTIONS, ,HEADINGS,SYMBOLS, ;NOM,TOL,MEAS,DEV,OUTTOL, , LOADPROBE/EPS 1X27_5 NO EXT TIP/T1A0B0, SHANKIJK=0, 0, 1, ANGLE=0 AUTOCALIBRATE/PROBE, PARAMETER_SET=EPS C504-002 1X27_5 NO EXT, QUALTOOL_MOVED=NO, CHECK COLLISION=NO, SHOW_SUMMARY=NO, OVERWRITE_RESULTSFILE=NO COMMENT/OPER,NO,FULL SCREEN=YES,AUTO-CONTINUE=NO, MOVE PROBE UP AND IN A SAFE POSITION. COMMENT/OPER,NO,FULL SCREEN=YES,AUTO-CONTINUE=NO, REMOVE THE CALIBRATION SPHERE AND RETURN IT TO THE HOME LOCATION.
Thanks!!!
Attached Files
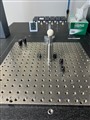