I can get the initial alignment (plane, line, point) and 'one hit' measure the diameter of several of the holes in the upper plate of this item. I then select three of these holes as my leapfrog alignment point groups. Set the probe comp OFF...start leapfrog...measure each feature five times per....then I rotate the part on the table about 90 degrees....select OK for re-positioning....re-measure each of the initial points (5 times per again)...accept the calculated measurement results...OK to insert leapfrog command...OK to close dialog box. Now I attempt to 1) measure another 'one hit' hole diameter and get "Hit Out Of Range" error. Then, I attempt to create a new plane entity and get the same message on the first hit to start defining the plane.
What am I doing WRONG???
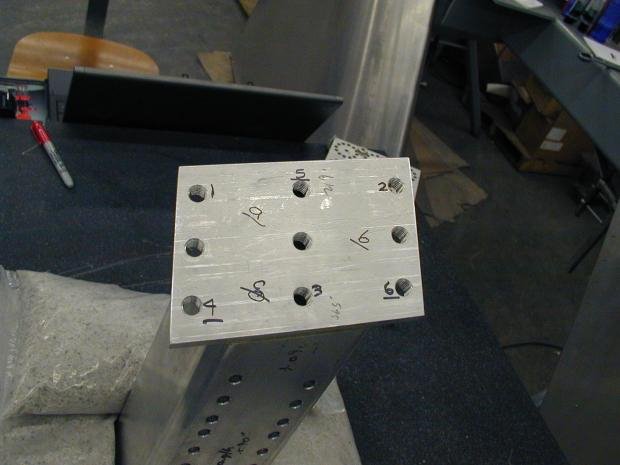


KJay