I attached a drawing the circled the dimensions that I want to check. Can this be down with just the vision probe? I currently have the part with the wide base laying flat on the glass so I can see the large ID in the center of the part. It has a tight tolerance so I need to check and I have not tried to check the part on its side.
Please let me know what ya'll think.
Attached Files
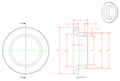