I prefer to use only negative A angles for my measuring routines for the following reasons:
- You can get the probe closer to the table. On our CMMs, with just 4" tall fixture plate standoffs I can raise the part enough to measure under it. The image below shows the lowest distance that can be reached on our Hexagon Bridge CMMs with the probe at two different angles that have the same probe vector.
- The probe does not swing around as much. For example, going from A90B90 to A-95B-90 will only change the probe orientation 5 degrees, but it will require a wild swing of the probe - what our CMM operators have named "Crazy Moves". It looks cool but it is not efficient and requires a lot of clearance.
- There is more clearance beneath the probe - Less likely to hit a fixture or something on the table.
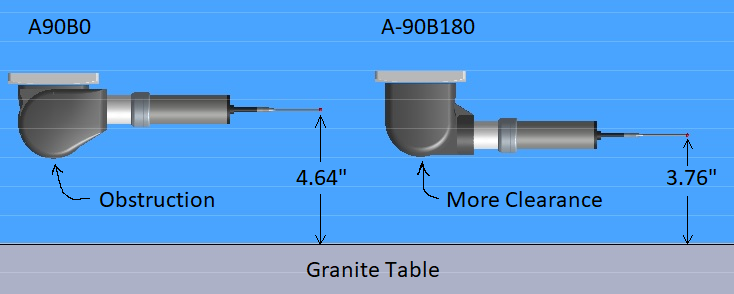
Attached Files
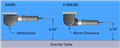