I'm trying to tolerance the 4x Ø4.49 holes on this part to datums [A][F], and have the following questions.
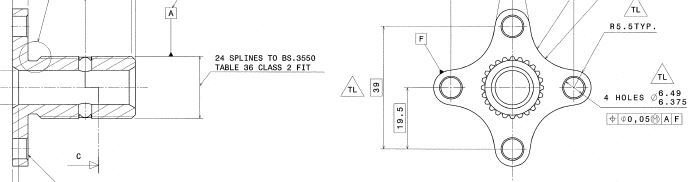
1. How do I create a best fit rotation as required for datum -F- (through the 4x R5.5)?
I have went ahead and completed the rest of the program and used a rotation between the left and right R5.5 in place of the best fit, and I am having issues with the reporting of the position and MMC.
2. How do I properly add MMB to the positional tolerance?
I have used the MMCADD evaluation within POSITNXY, and evaluated the diameter directly before this. See evaluations suffixed _LEFT, MMCADD should say 0.094, not 0.090, and it is not affecting the positional tolerance calculation. Where am I going wrong?
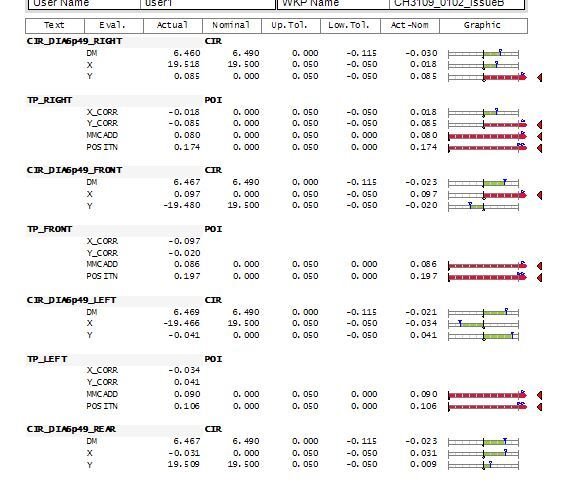
Thanks.