I am looking for some advice regarding a special characteristic that I need to find the intersection measurement between a generic circle/cylinder (R=34.5) and -0.49 below the part surface on an angled plane of 10+/-0.5 deg from the center of the measured circle (R= 30.25). The whole part is in 3D space, but the SC i am looking for is shown in 2D (ZX) as a side view. (hopefully the pic is visible).
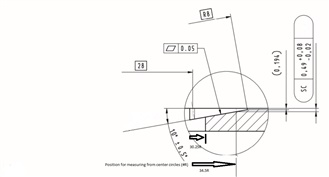
Ive experimented with different settings/methods for constructing lines, points, planes and generic constructions of cylinders/circles to try and program the needed measurement efficiently and accurately. I may be missing a step when trying to align the generic circle (34.5R @ Z-PLUS) to the smaller measured circle (which R=30.25) located below the angled plane. Another issue i have encountered is trying to create a stationary line from the center of the constructed circle intersecting at the desired measurement location (generic circle and angled plane intersection), in tolerance (0.49 +0.08/-0.02).
Please let me know if additional clarification. I am very grateful for any help and direction from the community