I made a very simple Iterative alignment program. I ran couple times, sometime it was good, but most pop out error message: Iterative Alignment Error. It is a very simple structure:
On plane A , there is a circle B and round slot C, I picked up 2 points beside B and C. Why it failed?
Thank you ( I uploaded the program and some images from the screen)
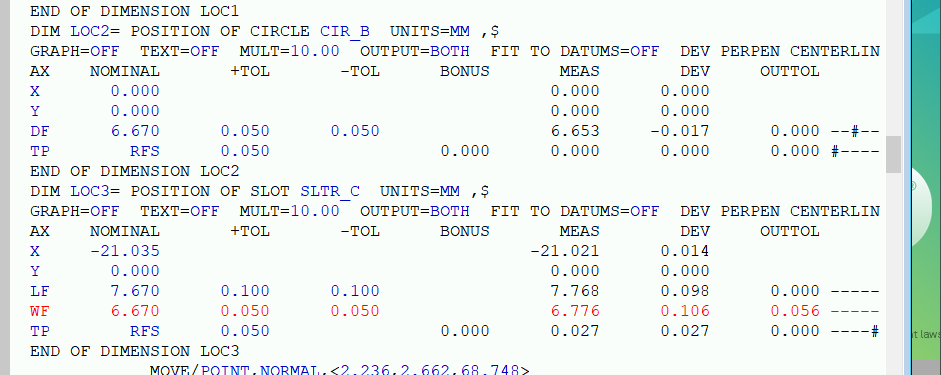
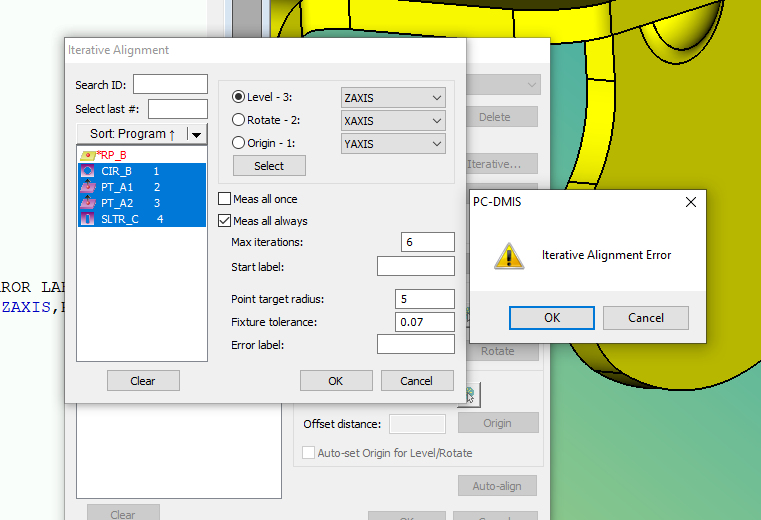
Attached Files