I use all auto features for scanning planes for flatness. So what ever the software decides is the what I use for speed.
One picture is the side of the probe. That's the one that has the circles on the probe. The other one is top down. That could either be the glue holding it onto the step, or a flat. Hard to tell im leaning twords the glue hold the ruby onto the stem.
Attached Files
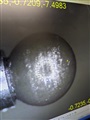
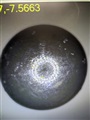