I've been digging into using a disc styli to measure a groove. I got everything programmed in 2019R2, and was checking the path lines. I noticed that when the probe moves to take a single hit on the depth of the groove, the prehit/retract will hit the top of the groove, by a lot. I adjusted the prehit/retract to .001", and I also removed the clearance plane and still no luck, it really didn't change anything.
I attached a couple pictures below for reference. I am probing the top circle first, then the groove diameter (no clearance plane) and then taking a single point for bottom of the groove (no clearance plane). I know the .001" prehit/retract is absurd, but I was just trying to see if I could get it to work at all.
I had no formal training in anything cmm programming, but have now been programming the CMM for 2 years (gotta love the "we'll hire a qualified person when the pandemic settles down more"). All my , learning has been from this forum, YouTube, or just trial and error, so i'm sure it's something simple i'm missing, I just can't quite figure this one out.
Any help would be appreciated.
Thanks
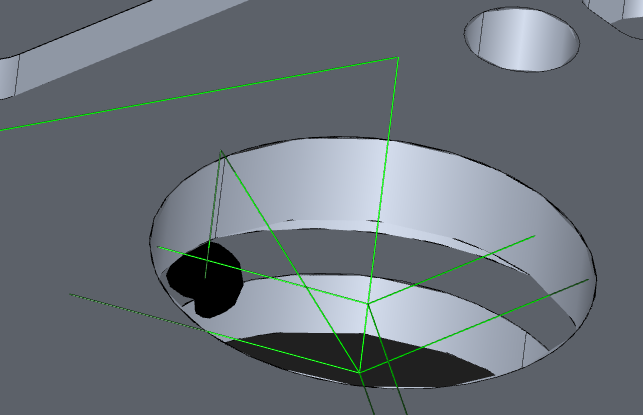
