Geometric Tolerancing in PCDMIS 2022 is relatively new to me, so I could be doing it wrong, but I've noticed that if I try to dimension a feature that is one of the datum's in the control frame, I get an error telling me I can't do it.
This feature is on a large part, so rotating it is not an option. Both the F and G cylinders are being scanned as circles at various depths. Cylinders are then constructed for both F and G.
So my questions are:
• Is this call out correct?
• If it is correct, how can I construct it to report correctly?
• If it's not correct, what's the best method to check this?
Attached Files
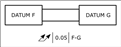