Came across this FCF earlier today and was wondering how to enter this into the FCF within my Program??
It allows me to choose A or B, but not both under the secondary datum (Or Primary Datum as shown further down in the photo)... Any help would be greatly appreciated. Thanks!!
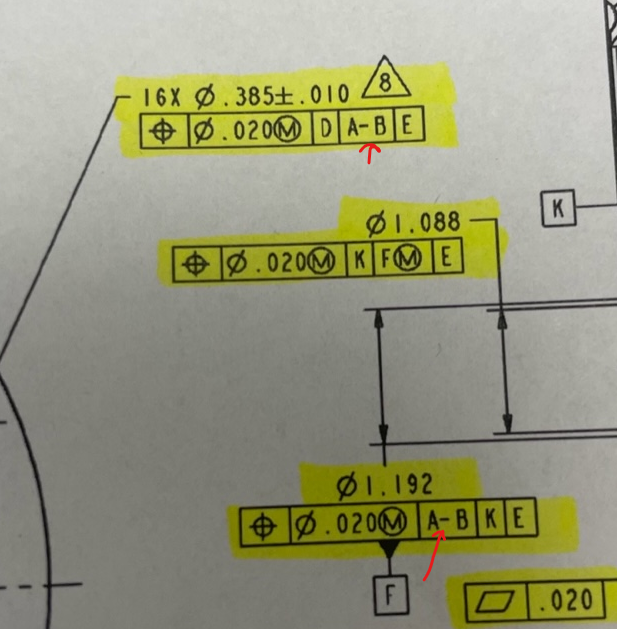