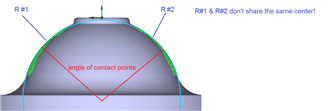
At the moment I use 3 scans to achieve this.
- One scan to evaluate the radius #1 (just the left side)
- One scan to evaluate the radius #2 (just the right side)
- One scan from left to right (over the top surface) to generate a contact circle which contacts a point left and right each to calculate the contact angle. I use the function "scan minimum" to create the contact circle.
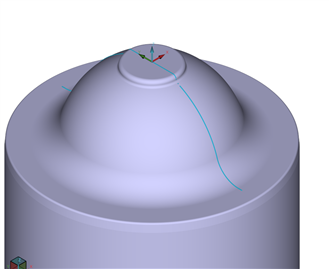
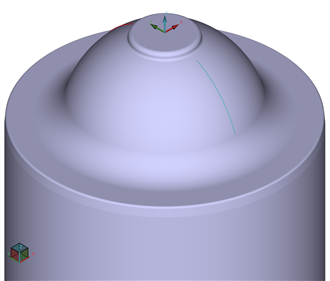
One problem I have, is that the scans are a bit rough/jittery. This results in the contact angle not being very stable.
What I want to do now is the following:
- get rid of the third scan from left to right
- filter the two separate radius scans
- generate the contact circle from the two filtered scans
The problem is, that the feature "scan minimum" doesn't allow me to input 2 separate scans.
I tried to generate a a set of the two scans and a point cloud to get around this limitation but nothing works.
Does somebody knows a way to get around this limitation? Maybe there is a way to feed all the pints into one scan?
If possible I would prefer a solution without a script but if necessary I would also resort to a script.