If I select "axis average" and enter .620 in the box on a cylinder, I can see the projected length in the dimension. I don't see that same thing if I use it on a circle. I'm using legacy for this in 2022.2. I've seen others say you can use it from a drop down box in Geometric Tolerancing, but I don't see an option for that in there.
Last question. Can you create a generic plane, dependent on the datum plane, add 0.62" to the location, then construct circles between the bolt hole pattern the generic projected plane to get the same result?
Either way, if someone could help me figure out the "right" way to do this, I'd appreciate it. See attached image please.
Thank you
Attached Files
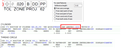