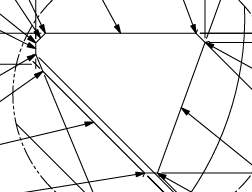
Any help is greatly appreciated.
Duane
Your Products have been synced, click here to refresh
Hi Dwade, I see your comments here and on the other place - I think maybe you're being maybe hasty in your criticism, and if I'm honest a little unfair.
I've read both threads through, and you don't mention what setting's you're using, which makes it difficult to fully consider what may be going on. You're saying it's BS but there might well be a valid explanation for what you're seeing, and it might serve as an opportunity to learn some of what's actually happening during the scanning process.
You do mention that you have 10 hits per 0.65 chamfer, this suggests a point density of ~15 points/mm? That seems like quite a high density, small changes in length of scan pass will therefore result in a greater change to the overall number of hits.
You also say that you have a profile result of up to 0.05 (i.e. possibly +0.025 per side) - For simplicity sake (and I know it's not quite right) but lets add 0.025 to each end of each side of your profile. this would equate to an increase in perimeter of 0.3mm which would equate 5 points straight away.
Also you don't mention what stylus you're using, perhaps the offline hits per mm is calculated by the cad surface perimeter, but the online hits is calculated by the distance the tip centre travels (for such a small shape this could be significantly larger).
I guess what I'm saying is, rather than just call BS, give us the relevant information, and together we can work out what's happening and work to resolve it.
Because it's what I'd term fairly intricate geometry, there may be things we can do to compensate - I'm thinking have a really high hit density, but then apply a very small linear filter (instead of NULLFILTER) to ensure a predictable spacing of hits around the feature.
Can you let us know:
Current Line 1 Tech type (NULLFILTER, LINEAR or VARIABLE).
Current point density (on the settings tab of the scan dialog)
Comp methods? I assume Probe Comp, but are you using CAD Comp as well?
Probe diameter.
OPTIONPROBE/MAXFORCE=0.096,LOWFORCE=0.019,UPPERFORCE=0.072,TRI GGERFORCE=0.033, PROBEACCURACY=0.1,POSACCURACY=0.1,#RETURNDATA=7, RETURNSPEED=0.4,[B]SCANPNTDENSITY=10[/B], SCANACCELERATION=10,SCANOFFSETFORCE=0.12, PROBINGMODE=DFL,MANFINEPROBING=NO
Hi Dwade, I see your comments here and on the other place - I think maybe you're being maybe hasty in your criticism, and if I'm honest a little unfair.
I've read both threads through, and you don't mention what setting's you're using, which makes it difficult to fully consider what may be going on. You're saying it's BS but there might well be a valid explanation for what you're seeing, and it might serve as an opportunity to learn some of what's actually happening during the scanning process.
You do mention that you have 10 hits per 0.65 chamfer, this suggests a point density of ~15 points/mm? That seems like quite a high density, small changes in length of scan pass will therefore result in a greater change to the overall number of hits.
You also say that you have a profile result of up to 0.05 (i.e. possibly +0.025 per side) - For simplicity sake (and I know it's not quite right) but lets add 0.025 to each end of each side of your profile. this would equate to an increase in perimeter of 0.3mm which would equate 5 points straight away.
Also you don't mention what stylus you're using, perhaps the offline hits per mm is calculated by the cad surface perimeter, but the online hits is calculated by the distance the tip centre travels (for such a small shape this could be significantly larger).
I guess what I'm saying is, rather than just call BS, give us the relevant information, and together we can work out what's happening and work to resolve it.
Because it's what I'd term fairly intricate geometry, there may be things we can do to compensate - I'm thinking have a really high hit density, but then apply a very small linear filter (instead of NULLFILTER) to ensure a predictable spacing of hits around the feature.
Can you let us know:
Current Line 1 Tech type (NULLFILTER, LINEAR or VARIABLE).
Current point density (on the settings tab of the scan dialog)
Comp methods? I assume Probe Comp, but are you using CAD Comp as well?
Probe diameter.
OPTIONPROBE/MAXFORCE=0.096,LOWFORCE=0.019,UPPERFORCE=0.072,TRI GGERFORCE=0.033, PROBEACCURACY=0.1,POSACCURACY=0.1,#RETURNDATA=7, RETURNSPEED=0.4,[B]SCANPNTDENSITY=10[/B], SCANACCELERATION=10,SCANOFFSETFORCE=0.12, PROBINGMODE=DFL,MANFINEPROBING=NO
© 2024 Hexagon AB and/or its subsidiaries. | Privacy Policy | Cloud Services Agreement |