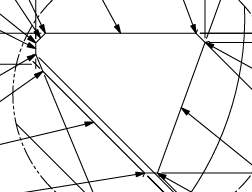
Any help is greatly appreciated.
Duane
Your Products have been synced, click here to refresh
dwade,
I see the number of points different you have posted elsewhere, and that seems extreme to me.
However, What Neil says is true in mCosmos and Calypso as well, as I have those and PcDmis here scanning in all three. If you want two hits per mm (.04") and your part has a perimeter that is 2 mm longer than the model, that would be an extra 4 hits.
With the delta you describe, and my best guess about actual size, I'm thinking you go from 23mm perimeter to 23.2-ish (based on the stated profile error if the part is bigger, 22.8-ish if smaller), so at 2/mm that would not even be one hit. I think you said something like 12-15 hits different.
What Neil describes, based on what I can guess, is not what you are experiencing. That doesn't make Neil wrong in what he said, though, as he doesn't know how many hits are missing, nor did he know your profile deviation.
In all three softwares, I can extract features so the points used are dynamic based on the actual scan (what Neil is suggesting), or I pump the density so that a few extra or missing hits don't wreck me on discreet point selection for constructions (what you appear to be doing).
I would never be able to live with 15 hits missing, though.
I can say, in Calypso, once, I had to re-select points after running a part online after programming offline because they were WAY off. Once. It is a machine we bought for a product family of 8 parts. Seven parts went from offline to online flawlessly. One part I had what you are having.
I didn't bother with the why, I changed my point selection and then it has worked ever since. Some artefact that the software saw in the model that isn't real, maybe, a seam that the software followed into the solid and back out that skewed my point count? I have no idea.
My point there is, I changed my point selection and it worked ever since. Can you do that?
If you run 10 parts, do they all have the same point count and distribution that this first part had? Maybe a single fix and you are good to go forever?
From the way mCosmos makes scan sections, I can visually see that the software follows seems into the model sometimes, and there is a method to trim that crap out. Maybe that is happening to you here, or something similar behind the scenes, and a one time adjustment will get you on track.
DAT_B =FEAT/CONTACT/CYLINDER/DEFAULT,CARTESIAN,IN,LEAST_SQR THEO/<40,30,0>,<0,0,1>,30,10 ACTL/<39.996,30.009,0>,<-0.000369,0.0003466,0.9999999>,29.933,10 TARG/<40,30,0>,<0,0,1> START ANG=0,END ANG=360 ANGLE VEC=<1,0,0> DIRECTION=CCW SHOW FEATURE PARAMETERS=NO SHOW CONTACT PARAMETERS=YES NUMHITS=7,NUMLEVELS=3,DEPTH=1,END OFFSET=2.1,PITCH=0 SAMPLE METHOD=SAMPLE_HITS SAMPLE HITS=0,SPACER=0 AVOIDANCE MOVE=BOTH,DISTANCE BEFORE=10,DISTANCE AFTER=10,DIRECTION=ALONG FEATURE VECTOR FIND HOLE=DISABLED,ONERROR=NO,READ POS=NO SHOW HITS=NO $$ NO, hit density 4 pnts/mm ASSIGN/PI=4*ATAN(1) ASSIGN/CIRCUMF=DAT_B.D*PI ASSIGN/CIRCNUMHITS=CIRCUMF*4 ASSIGN/OFFLINEHITS=376 $$ NO, 4mm tip gives a 26mm tip centre diameter ASSIGN/DIAM_PRB_CENT=26 ASSIGN/CIRCUMF_CENT=DIAM_PRB_CENT*PI ASSIGN/ONLINEHITS=CIRCUMF_CENT*4 ONLINE_SCAN=FEAT/SCAN,LINEARCLOSE,NUMBER OF HITS=325,SHOW HITS=NO,SHOWALLPARAMS=NO MEAS/SCAN BASICSCAN/LINE,NUMBER OF HITS=325,SHOW HITS=NO,SHOWALLPARAMS=NO ENDSCAN ENDMEAS/ OFFLINESCAN=FEAT/SCAN,LINEARCLOSE,NUMBER OF HITS=376,SHOW HITS=NO,SHOWALLPARAMS=NO MEAS/SCAN BASICSCAN/LINE,NUMBER OF HITS=376,SHOW HITS=NO,SHOWALLPARAMS=NO ENDSCAN ENDMEAS/
Hi Dwade, I see your comments here and on the other place - I think maybe you're being maybe hasty in your criticism, and if I'm honest a little unfair.
I've read both threads through, and you don't mention what setting's you're using, which makes it difficult to fully consider what may be going on. You're saying it's BS but there might well be a valid explanation for what you're seeing, and it might serve as an opportunity to learn some of what's actually happening during the scanning process.
You do mention that you have 10 hits per 0.65 chamfer, this suggests a point density of ~15 points/mm? That seems like quite a high density, small changes in length of scan pass will therefore result in a greater change to the overall number of hits.
You also say that you have a profile result of up to 0.05 (i.e. possibly +0.025 per side) - For simplicity sake (and I know it's not quite right) but lets add 0.025 to each end of each side of your profile. this would equate to an increase in perimeter of 0.3mm which would equate 5 points straight away.
Also you don't mention what stylus you're using, perhaps the offline hits per mm is calculated by the cad surface perimeter, but the online hits is calculated by the distance the tip centre travels (for such a small shape this could be significantly larger).
I guess what I'm saying is, rather than just call BS, give us the relevant information, and together we can work out what's happening and work to resolve it.
Because it's what I'd term fairly intricate geometry, there may be things we can do to compensate - I'm thinking have a really high hit density, but then apply a very small linear filter (instead of NULLFILTER) to ensure a predictable spacing of hits around the feature.
Can you let us know:
Current Line 1 Tech type (NULLFILTER, LINEAR or VARIABLE).
Current point density (on the settings tab of the scan dialog)
Comp methods? I assume Probe Comp, but are you using CAD Comp as well?
Probe diameter.
OPTIONPROBE/MAXFORCE=0.096,LOWFORCE=0.019,UPPERFORCE=0.072,TRI GGERFORCE=0.033, PROBEACCURACY=0.1,POSACCURACY=0.1,#RETURNDATA=7, RETURNSPEED=0.4,[B]SCANPNTDENSITY=10[/B], SCANACCELERATION=10,SCANOFFSETFORCE=0.12, PROBINGMODE=DFL,MANFINEPROBING=NO
© 2024 Hexagon AB and/or its subsidiaries. | Privacy Policy | Cloud Services Agreement |