Fast question for the following callout:
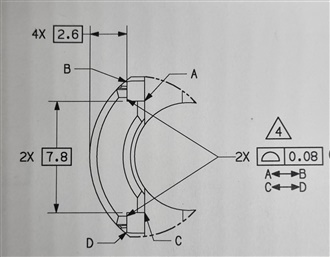
The callout is for controlling these 2 "L" shaped pockets(?!). This is actually half the part as there is a mirror half on the right side (thus the 2x and 4x designations on the basic dimensions). I am a bit confused as the 2.6 basic dimension is restricting translation of the vertical planes while the callout has no datums in the callout. Is this correct?
How would you control this in a no CAD program? Thanks in advance for your advices