Is there a way to soften those machine lines for the vision to grab the thin black shadow that is near the crosshairs?
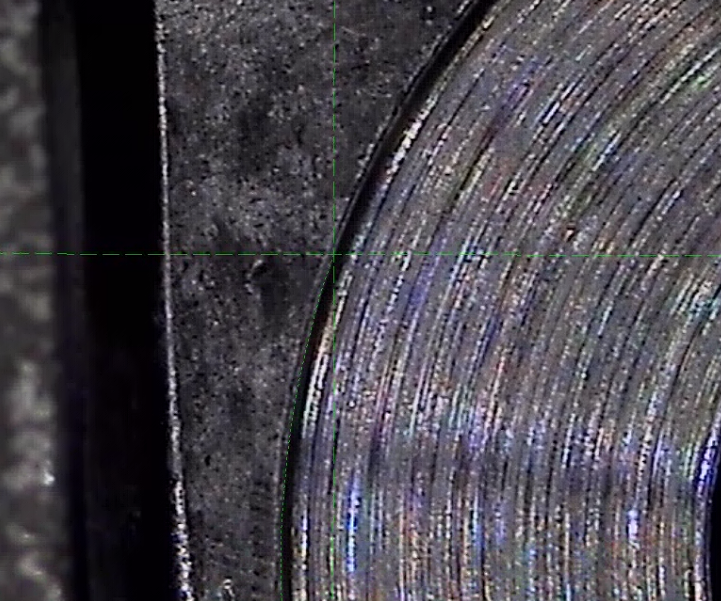
Your Products have been synced, click here to refresh
I'm not at the cmm, you can choose theindicated edge, the major" edge...
In one of those choices, you can indicate the number of the edge that you want.
If you choose searching from blak to white, out to in, first edge, you should find the right one...
Heh, happy to see that we have all the same difficulties on our optivs...![]()
I'm often confronted to this, but like you i play with the detection options to find the "least bad" setting...
Or, like you said, just turn to manual, using tiny targets to place by the user. After all, there is no harm to do it, the goal is to have the real edge. Sometimes i even mark the edges with some pen, especially on white parts.
Anyway, i realize that it's pretty difficult to have repeatable measurements in visio !
I mean, last week i began to validate a new 2D vision machine with a Type1 R&R (not done yet), and decided to apply it before on the Optiv just to see. I took 50 consecutive measurements on a 6mm calibrated ring, looks pretty easy on black/green contrast, but huh, there are sometimes 0.008mm gap between measures... R&R fails![]()
I'm pretty sure that just by changing the illumination (going a bit overexposed) i'll divide the gap, but heh, hard to explain that to the quality guys !
Let's be happy, look like visio machines will never replace our eyes
© 2025 Hexagon AB and/or its subsidiaries. | Privacy Policy | Cloud Services Agreement |