I have a part that the drawing only given a couple of FCF for True Position for 4 holes, Angle related to Datum A B &C and a profile tolerance of .030. I have to use a CAD model for inspection.
I was able inspecting the holes. For the remaining periphery of the parts, have been told because Profile Tolerance was given, I have to use a feature in PC-DMIS to inspect the periphery of the part, include angles. Please see the picture attached.
I am newbie to Romer Arm and PC-DMIS and working Profile Tolerance. Your guidance is greatly appreciated.
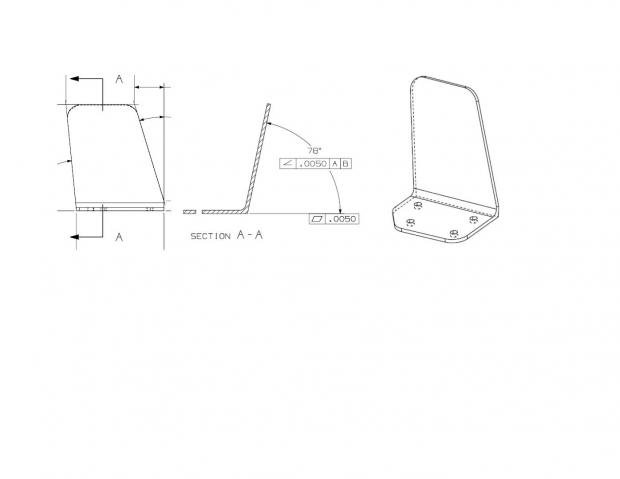