Attached Files
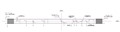
Your Products have been synced, click here to refresh
Assuming your A1/A2 line runs along the Y axis:
Level axis line Yplus/minus (2 DOF)
Rotate B about line (1 DOF) <-most likely rotate to Zplus as required about Y
Origin line - X/Z (2 DOF)
Origin B - Y (1 DOF)
That will handle the 6 DOF.
In my opinion, you should start with collecting the cylinders making a temp axis from those manual inputs, then measure B and complete the temporary alignment. Now repeat the process with DCC and beef up the hits used. This should enable you to have a good foundation to move forward with.
© 2024 Hexagon AB and/or its subsidiaries. | Privacy Policy | Cloud Services Agreement |